FORTUNE magazine
March 1975
In an era of increasingly high-priced energy, the old-fashioned techniques used by Leslie Salt Co. of Newark, California, look like a very attractive technology. The manufacture of salt by solar evaporation was mentioned in the Bible, and centuries before Leslie set up its own operation on San Francisco Bay the Ohlone Indians were harvesting salt from similar mud flats and marshes nearby. Today the company still relies mainly on the sun and the wind to convert seawater into salt, a commodity that is essential to many industries and, indeed, to life itself.
As befits one of the worlds largest producers of salt by solar evaporation, Leslie operates with well-studied sophistication. To produce one million tons of salt annually, it pumps nearly ten billion gallons of seawater each year into a maze of ninety ponds that stretches for twenty-five miles around the southern tip of San Francisco Bay. The six-inch layer of giant crystals found at the bottom of the final crystallization pond (opposite page) is the product of a five-year process, during which water of normal salinity (about
3 percent) from the bay is progressively converted into a supersaturated solution that is 25 percent salt. The draining of the final pond has to be precisely timed, because the concentration must be stopped before other chemicals, including magnesium and bromine salts, crystallize and add unwanted impurities to the "pickle." And this harvest, like many another, can be spoiled by too much rain.
One byproduct of the process is the catch of small fish washed into the ponds with the bay water; Leslie sells these as bait to sports fishermen. Saltier ponds yield tiny brine shrimp that provide fish food for aquariums. And millions of migratory birds including pintail and canvasback ducksfeed in the salt marshes each winter.
|
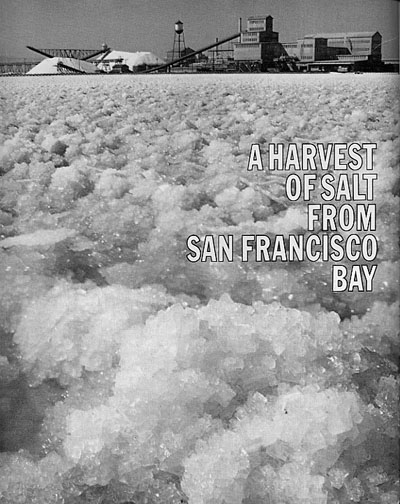 |
The fate of those birds became a source of contention a few years ago, when Leslie was trying to develop some of its land as a housing tract. Partly because of ecologists objections, the project ran into delays that cost the company $8 million. Finally, Leslie agreed to sell 38,000 of its 47,000 acres to the Trust for Public Land, a local nonprofit group, for $17.9 million. The trust expects to resell the property to the federal government as part of a national wildlife refuge.
Leslie will retain 4,500 acres of land for its plant and will keep the right to maintain its evaporation ponds in the wildlife refuge (see map below). Having made peace with the ecologists, the company plans to sell a few inland parcels of land for parks and industrial development. |
 |
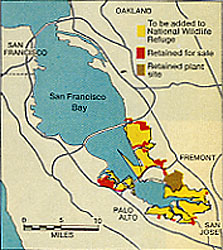
These arent wheat fields; they are ponds of briny water at Leslie Salt Co.s operation on San Francisco Bay. Different concentrations of salt encourage the growth of particular types of algae, giving each pond a distinctive color. |
 |
Like an icebreaker, this specially designed harvester (below) rips up the six-inch crust of salt and deposits the nearly pure sodium chloride crystals in a small train that takes twenty-two tons at a time to a washing plant. Then gantrys heap the salt into 100-foot piles like the one shown on the facing page. Familiar landmarks to Bay Area residents, they resemble ski slopes, with a trail from the top carved by a bulldozer, which pushes the salt back into carts as it is needed. Highest in December, just after the salt harvest, the piles shrink throughout succeeding months as Leslie draws on its inventory. The salt is sold in the West, since the cost of transportation is higher than the cost of production. Leslie now supplies its export markets from a 1.3-million-ton plant near Port Hedland, Australia, where better weather conditions cut the five-year evaporation cycle to eighteen months. |
Narrow-gauge tracks for the wooden trains are light
and portable, so they are moved as the harvester cuts thirteen-foot swaths through the crystallization ponds. Aside from the trains diesel fuel and a bit of electricity for lights, about the only energy that the company has to pay for is natural gas
used in the drying kilns (right). Only about 160,000 tons
a year go through this stage. Most of the salt is sold in crude form for use in manufacturing plastics, soap, explosives, and fertilizer. Kiln-dried salt is screened by size and used, among other things, for water softening, fish packing, and animal feed. The company also sells salad dressings and sauces, but
salt provided about 90 percent of last years approximately $37 million in sales and about the same share of the estimated
$3.7 million in pretax profits. |
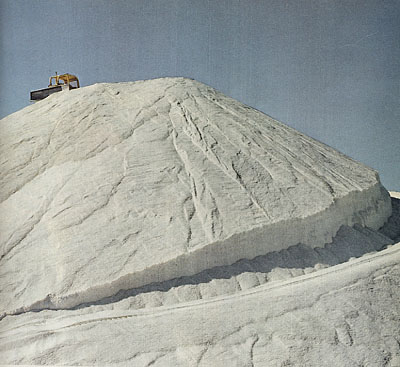 |
A household name to Westerners, Leslie Salt Co. processes 8,600 tons a year of its millionton output for sale in these familiar cardboard cartons (right) as common table salt. |
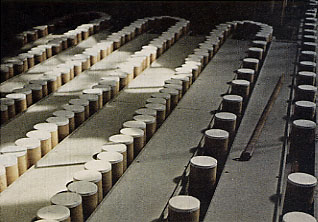 |
|
 |